Design engineers of Aerospace propulsion systems are always challenged with optimizing the performance of their system. As program requirements firm up, system design engineers canvass the industry to ascertain the availability of components that can improve the system performance. One of the areas for improvements are check valves. Check valves prevent the backflow of process media in hydraulic, propellant and oxidizer systems. Check valves have a reputation as being problematic in operation. However, this is often due to misapplication of the device.
Chatter normally occurs in spring biased check valves when the valve poppet opens quickly and begins to oscillate against the seat. Prolonged chattering will lead to premature seat destruction and resulting valve leakage under reverse flow conditions. This leakage renders the check valve non-functional, and it must be replaced. Chatter is frequently the result of an oversized check valve, as there is insufficient flow to keep the poppet off of its seat during normal operation. High velocity flow can also create conditions that lead to chattering. Properly sized check valves should not chatter during normal flow conditions. Still, should flows drop substantially while in service, then the check valve might chatter. Valcor utilizes a proprietary construction that provides stable, chatter-free operation under all flow and pressure conditions. The unique design dampens the poppet’s movement, allowing it to move to the fully open position without rebounding, or oscillating under low flow conditions that might create the chatter. Valcor’s check valves are flight-proven, having flown on many spacecraft missions.
There are many factors to consider when sizing a check valve; using the process line size alone is not sufficient, nor desirable. Factors such as fluid temperature, pressure, viscosity and turbidity all affect the sizing of a check valve. Based on the rigors of the application, choosing the seat material will also affect the long-term performance of the check valve. Soft vs hard seats and allowable leakage (if any) under reverse flow conditions should also be taken into consideration. In rare instances, the fast closing and opening of valves or other downstream devices can create a shock wave in the fluid that can trigger a check valve to chatter. In this case, Valcor’s proprietary design will protect the check valve from reacting to this shock force. The all-welded construction eliminates the potential for external leakage, even under the most demanding shock and vibe conditions.
In critical flight applications, it is often desirable to provide as much redundancy in the fluid control system as possible without compromising weight and space constraints. Valcor offers a compact, redundant check valve assembly incorporating two check valves in series. If for any reason one check valve is not operating properly, the other will continue to provide protection against a reverse flow condition. The redundant check valve assembly is available with an optional test port between the primary and secondary checks, enabling technicians to conduct pre- and post-flight system testing.
Check valves are used for many applications in ground-based and on-board fluid control systems, including propellant control for Reaction Control Systems (RCS) and Attitude Control Systems (ACS). Let Valcor’s highly trained and experienced Application Engineers size our single and redundant check valves to meet the specifications of your system design today!
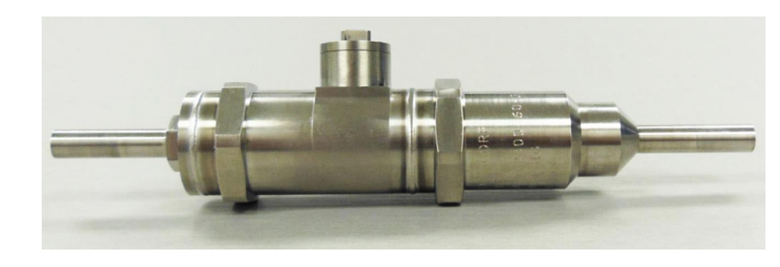
Valcor’s V2300 Series Redundant Check Valve Assembly
Recent Comments